Offsite, prefab, and modular are three related methods of construction that have gained popularity in the building industry. Yet the terminology is not always clear cut, since the three terms are often used interchangeably.
If you’ve recently come across an article or a video about one of these methods, you might find yourself wondering—can a building made of modular units contain prefabricated elements? Can some components be made off site while the rest of the structure is built using traditional methods?
In this article we’ll attempt to shed light on some key differences and similarities between these construction methods in the hopes of demystifying this topic for you. Let’s jump right in.
What is Offsite Construction
The NIBS defines offsite construction as “the planning, design, fabrication, and assembly of building elements at a location other than their final installed location”.
Offsite construction is a catch-all term, which, depending on the context, can apply to both modular construction and prefabrication. It refers to construction processes where individual components of a building or completed sections are manufactured in a factory and installed on the construction site.
A complete section of a building that was manufactured in a factory is also called a module. This could be an entire office room with walls, floors, and lighting fixtures—all manufactured and assembled inside a factory, then transported, stacked, and fitted in place at the job site.
More prevalent is the method of using pre-built components such as walls and floor panels. These individual components are manufactured off-site, and installed in place, while the rest of the structure is built with traditional on-site methods. This offers greater flexibility when building projects such as shopping malls or airports, which do not use modules.
In other words, every project can take advantage of the benefits offered by offsite construction, such as increased quality control and leaner completion times.
What construction materials are used in offsite construction?
Offsite, prefab, and modular construction projects generally rely on light gauge steel (or cold-formed steel), wood, and concrete. More specifically, the core frame of a building is built with light gauge steel or wood.
In North America, residential buildings typically use a greater percentage of wood, while commercial buildings use more light gauge steel. This will vary depending on your region and climate. Sweden and Japan, for example, are world leaders when it comes to building prefabricated, single-family housing units with wood.
Read about the implications of offsite construction for the future of construction:
What is Prefab or Prefabrication
Prefab or prefabrication is also arguably the term most confused with offsite construction. It refers to the process of manufacturing individual components (as opposed to modules) at a factory, which are then transported on-site site for installation.

Pictured above is a truck carrying stacks of light gauge steel studs, which will be used to create the wall panels for a mixed-use project. These prefabricated components are packed together and ready to be transported to the construction site—a sight sure to make any offsite builder’s day.
Prefab components can include wall panels, roof trusses, floor panels, or cassettes. They are standardized which allows them to be used in various pre-designated areas of a building. At the same time, they are not customized to the same degree as modular units.
Modular Construction
The MBI defines modular construction as “a process in which a building is constructed off-site, under controlled plant conditions using the same materials and designing to the same codes and standards as conventionally built facilities”. The first part may sound awfully similar to the various definitions of offsite construction that are available online.
Modular construction as a term however is typically used for projects that require a high degree of repetition or standardization, including multi unit residential buildings, hotels, student housing.
As the name suggests, this construction method involves building entire ‘modules’, which are completed units that may also include finished interior and exterior walls, floors and other components, that are stacked like lego blocks, or jenga blocks.
We may come across terms like volumetric modular, meaning three dimensional modules that are finished and ready to be installed, as mentioned above. It is also used to distinguish from ‘panelized construction’, where individual sections such as wall panels and floors are fitted together on-site.
Many of us will use modular construction and prefabrication synonymously. However in this scenario, it would imply panelized construction or a ‘kit of parts’, that is prefabricated off-site, as opposed to a three dimensional module. We hope that wasn’t too confusing.
What are some best practices when starting out with modular construction?
Tiago Atwi, Co-founder at the US Frame Factory anwers this question for us. There are a few key details that need to be addressed before you begin your first modular/prefab project according to Tiago, and these are:
Transport
The first thing to consider is how you will transport and move the modules. This phase can lead to significant costs due to oversized trucking fees and the rental of a heavy crane for module placement. The initial step should involve commissioning an engineer to design a lift plan for your modules.
An Engineered Lift Plan will determine the crane size, establish lift points on your modules, and outline rigging and reinforcement options.
On site installation
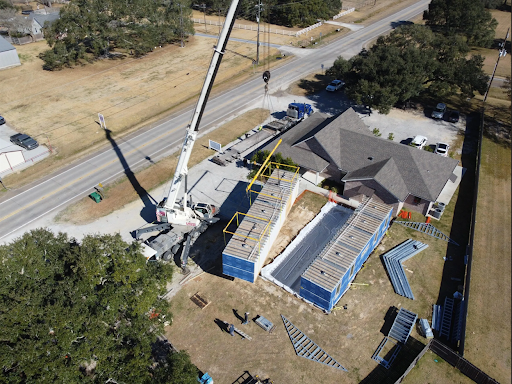
You want to ensure that your modules are structurally robust for lifting without overbuilding them. Typically, the most substantial cost of module construction lies in the structural components (such as iron I beams for reinforcement and costly load-bearing lumber).
Structural engineers, particularly in emerging industries, may tend to overdesign. Having an experienced modular contractor review your plans can potentially save you a significant amount of money on labor and materials.
MEP and HVAC connections
Another consideration involves on-site HVAC, electrical, and plumbing connections. Although the majority of the work is done in the factory, on-site connections for these trades are inevitable.
A common design oversight is failing to leave enough space in the assembled building for HVAC Supply Air ducts. This can be prevented by having both the HVAC engineer and HVAC installers review your plans before construction commences.
Discover digital construction solutions for offsite builders
For more information on our products or design services, visit strucsoftsolutions.com, or email us at info@strucSoftsolutions.com